Machining of High-Entropy Alloy Components: Challenges and Opportunities
Machining of High-Entropy Alloy Components: Challenges and Opportunities
Introduction
High-entropy alloys (HEAs) are a novel class of metallic materials composed of five or more principal elements in near-equal proportions. Their unique combination of strength, hardness, heat resistance, and corrosion resistance makes them attractive for aerospace, energy, and defense industries.
However, machining HEAs presents significant challenges due to their complex composition and physical properties. These alloys can cause excessive tool wear and require adapted machining strategies.
Key Machining Challenges
1. High hardness and strength
HEAs often exhibit hardness above 400–500 HV and tensile strength over 1000 MPa. This results in increased cutting forces and accelerated tool wear.
2. Low thermal conductivity
Heat accumulates in the cutting zone, leading to thermal overload of both the tool and the workpiece. Efficient cooling is essential.
3. Anisotropy and microstructural inhomogeneity
Some HEAs show unstable machining behavior due to alternating soft and hard zones, causing chatter, tool vibration, and poor surface finish.
Strategies and Solutions
Tool selection
-
Carbide tools with nano-coatings (e.g., TiAlN, AlCrN)
-
CBN and ceramic inserts for finishing
-
DLC or diamond-like coatings for softer HEAs
Optimized cutting parameters
-
Reduced feed rates and speeds (typically 20–40% lower than standard alloys)
-
Shallow cuts with stable tool paths
Efficient cooling methods
-
High-pressure coolant systems (HPC), MQL
-
In some cases: dry cutting with high-performance tool geometry
Comparison with Other Materials
Material | Machinability | Remarks |
---|---|---|
High-strength titanium | ★★☆☆☆ | Low thermal conductivity, high wear |
Stainless steel 316 | ★★★☆☆ | Good with coolant |
Inconel (Ni-superalloy) | ★☆☆☆☆ | Extremely tool-wearing |
HEA (e.g., CoCrFeMnNi) | ★★☆☆☆ | Poor machinability, requires adjustment |
Future Outlook
HEAs represent the future of structural materials for extreme environments. Unlocking their potential in manufacturing requires:
-
Development of custom tool materials and coatings
-
Precision machining with real-time process monitoring
-
Integration of hybrid machining methods (e.g., laser-assisted, EDM + milling)
Conclusion
Machining high-entropy alloys is demanding, but with the right tools, cutting parameters, and cooling strategies, it can be mastered. Ongoing R&D efforts continue to improve the feasibility of HEA processing in industrial environments.
Nanocoatings for Cutting Tools: Durability and Wear Resistance
Nanocoatings for Cutting Tools: Durability and Wear Resistance
Introduction
-
Modern metalworking requires precision and tool stability
-
Tool edge wear causes downtime and part defects
-
Solution: Nanocoatings that significantly extend tool life
What Are Nanocoatings?
-
Ultra-thin (tens of nanometers) multi-layer coatings
-
Applied using PVD or CVD technologies
-
Made of hard compounds: nitrides, carbides, oxides
-
Typically consist of 2–7 layers, each under 100 nm thick
Advantages of Nanocoatings
-
Improved Wear Resistance
-
Protects cutting edge from abrasive and adhesive wear
-
-
Reduced Friction
-
Lowers cutting forces and heat generation
-
-
Resistance to Aggressive Environments
-
High chemical and oxidation stability
-
-
Extended Tool Life (2–5×)
-
Especially effective with hardened steels, titanium, superalloys
-
Types of Nanocoatings
Coating | Composition | Key Features |
---|---|---|
TiAlN | Titanium-Aluminum Nitride | Great heat resistance, universal use |
AlTiN | Inverted Ti/Al ratio | Ideal for high-speed cutting |
CrN | Chromium Nitride | Strong corrosion resistance |
DLC | Diamond-Like Carbon | Ultra-low friction, great for non-ferrous metals |
nACo® | Nanocomposite TiAlN/Si₃N₄ | Exceptional thermal and wear resistance |
Deposition Technologies
-
PVD (Physical Vapor Deposition)
-
Low temp, eco-friendly, excellent adhesion
-
-
CVD (Chemical Vapor Deposition)
-
Better for deep coverage and larger tools
-
-
Emerging: HiPIMS, ALD, nano-laminates
Examples & Case Studies
-
TiAlN-coated tools: +300% life when milling stainless steel
-
DLC coatings: minimize wear with copper/aluminum
-
Turning Inconel-718: nanocoated inserts allow higher feed and fewer vibrations
Choosing the Right Coating
Workpiece Material | Recommended Coating |
---|---|
Carbon Steels | TiAlN, AlTiN |
Titanium Alloys | nACo, AlTiN |
Aluminum, Copper | DLC, CrN |
Heat-Resistant Alloys | nACo, multi-layer AlTiN |
Future of Nanocoatings
-
Self-healing surfaces
-
Smart coatings that adapt to heat/load
-
Hybrid layers (PVD + ALD)
-
Nano-friction management technologies
Conclusion
-
Nanocoatings reduce tool cost and increase machining reliability
-
A well-chosen coating means better performance, less downtime
-
The future lies in adaptive and eco-friendly nanoengineering
Eco-Friendly Cutting Fluids: Bio-Based Oil Alternatives
Eco-Friendly Cutting Fluids: Bio-Based Oil Alternatives
Introduction
-
Cutting fluids (coolants/lubricants) are essential in metalworking
-
Traditional fluids pose health, disposal, and environmental challenges
-
Green technologies are gaining traction in industrial settings
Why bio-based fluids?
-
Derived from plant sources: soy, rapeseed, sunflower, palm
-
Biodegradable and non-toxic
-
Reduce waste disposal costs and improve workplace safety
Types of bio-based cutting fluids
-
Pure vegetable oils
-
Pros: simple, eco-friendly
-
Cons: limited shelf life, oxidation risks
-
-
Emulsifiable bio-fluids
-
Oil-water mixes for better cooling and versatility
-
-
Synthetic esters of fatty acids
-
More stable, longer-lasting, high thermal resistance
-
Comparison Table
Parameter | Mineral Oils | Bio-Based Fluids |
---|---|---|
Environmental impact | High | Low |
Purchase cost | Lower | Higher (but pays off) |
Tool life | Moderate | Often longer |
Disposal | Requires treatment | Biodegradable |
Implementation challenges
-
Initial cost
-
Equipment compatibility
-
Storage sensitivity
Examples
-
Audi, Bosch use rapeseed-based coolants
-
DMG Mori offers machines optimized for bio-fluids
-
Workshops in Germany and Scandinavia making the switch
Future trends
-
Universal bio-fluid development
-
Monitoring systems for pH and microbial stability
-
Closed-loop recycling systems
Conclusion
-
Bio-fluids are a viable, sustainable alternative
-
With proper implementation, they are both eco- and cost-effective
Top 10 Ultrasonic & Precision CNC Machining Centers
Top 10 Ultrasonic & Precision CNC Machining Centers
1. DAMA.ch Ultrasonic Micro Machining Systems
Switzerland
Leaders in ultra-precision ultrasonic machining for micro-scale components in optics, MEMS, ceramics, and glass. Offers nanometer-level surface finishes and sub-micron tolerances, ideal for R&D and high-tech industries.
2. Conprofe Ultrasonic CNC Centers (ULM Series)
China
Advanced 3- and 5-axis CNC machines with 16–60 kHz ultrasonic vibration. Designed for machining hard and brittle materials like sapphire, ceramics, glass, and carbon fiber. Eco-friendly, high-efficiency systems gaining global adoption.
3. DMG MORI Ultrasonic / LASERTEC Series
Germany / Japan
High-end 5-axis ultrasonic and hybrid machining centers for aerospace, optics, and medical industries. Known for automation integration and precision.
4. Yamazaki Mazak (Variaxis & Integrex)
Japan
Multi-tasking high-precision CNC systems with excellent thermal stability and 5-axis versatility.
5. Makino PS / T-Series
Japan
High-speed and high-precision machining for aerospace and mold-making. Offers thermal compensation and nanometer-level repeatability.
6. GF Machining Solutions (Mikron, AgieCharmilles)
Switzerland
Renowned for micromachining and EDM, widely used in medical devices, watchmaking, and electronics.
7. Okuma MB & Multus Series
Japan
Reliable and rigid CNC platforms with thermal-friendly design. Excellent for complex large-part machining.
8. FANUC Robodrill + Automation
Japan
Compact, high-throughput CNC centers with optional ultrasonic tool compatibility and full robotic integration.
9. Starrag (NB / LX / STC Series)
Switzerland
Specialized in turbine blades and structural aerospace parts with very high dynamic precision.
10. Mandelli Sistemi SPARK Series
Italy
Horizontal and multi-axis machining centers with exceptional rigidity, ideal for automotive and aerospace applications.
How to Automate Workpiece Loading: Solutions for Small Workshops
How to Automate Workpiece Loading: Solutions for Small Workshops
In small and medium-sized manufacturing workshops, automation is often seen as expensive or inaccessible. However, one of the most labor-intensive tasks — loading and unloading workpieces — can already be automated today without huge investments. Modern solutions help improve productivity and reduce equipment wear, even within tight budgets and limited space.
Why Automate Workpiece Loading
Problems with manual loading:
-
Human error and fatigue
-
Breaks, downtime, and inconsistent feed
-
Limited cycle speed
-
Unstable quality due to imprecise placement
Benefits of automation:
-
Stable production rhythm
-
Fewer mistakes and rejects
-
Operation in semi-automatic or unattended mode
-
Better machine return on investment
-
Lower labor costs
Automation Options for Small Enterprises
1. Gravity and vibratory feeders
Simple devices for feeding small parts like bolts or washers.
-
Hopper and chute systems
-
Suitable for series production
-
Price range: €500–€2,000
2. Pneumatic feed systems
-
Suitable for medium-sized workpieces
-
Simple design, low energy use
-
Can be added to older CNC machines
3. Manipulators and low-cost collaborative robots (cobots)
-
Cobots can load and unload parts or perform sorting
-
Safe to operate next to humans
-
Starting from €12,000
-
Ideal for small batch or single-piece production
4. Linear gantry systems
-
Compact bridge-like mechanisms above machines
-
Effective for repetitive operations
-
Space-saving
-
Easily reconfigurable
5. Automatic carousel systems and pallet changers
-
Preload workpieces onto pallets
-
Automatically feed them into the machine
-
Enable continuous unattended operation
How to Choose the Right Solution
Question | What to Consider |
---|---|
Type and size of parts | Weight, shape, and dimensions |
Production volume | Single, small-batch, or series |
Available space | Access, layout, and utilities |
Budget | Is phased implementation possible? |
Production flexibility | Is frequent changeover needed? |
Step-by-Step Implementation Strategy
-
Analyze current manual operations
-
Choose a pilot machine or work area
-
Select a suitable automation solution
-
Consider safety and certification
-
Train personnel to use the new system
-
Measure results and compare before/after data
Example from Practice
A workshop with three CNC machines and two operators was losing time on manual loading, especially later in shifts.
Solution:
A low-cost robotic arm with a dual gripper was installed.
Outcome:
-
Output increased by 28%
-
Reject rate decreased by 14%
-
Return on investment within 9 months
Conclusion
Automating workpiece loading is a smart step for even small manufacturers. Affordable and compact solutions now make it realistic to transition toward a smarter, more competitive production process.
Integrating IIoT into Metalworking: Benefits and First Steps
Integrating IIoT into Metalworking: Benefits and First Steps
In the age of industrial digital transformation, manufacturers increasingly turn to IIoT (Industrial Internet of Things) technologies. A particularly promising area is the integration of IIoT into the metalworking industry, where efficiency, reliability, and precision are key.
What is IIoT and Why Use It in Metalworking?
IIoT connects industrial devices, machines, sensors, and software into a unified system that collects and analyzes data in real time. This helps:
-
monitor equipment 24/7,
-
prevent breakdowns,
-
optimize machine usage,
-
analyze production processes.
Example:
A CNC machine reports data on spindle temperature, load, vibration, and cycle time. This data is processed in the cloud, and alerts are sent to a technician when anomalies are detected — before failure occurs.
Key Benefits
-
Reduced Downtime – Predictive maintenance prevents unscheduled stops.
-
Increased Productivity – Identifying bottlenecks improves efficiency.
-
Resource Savings – Smarter use of energy, coolant, and tools.
-
Transparency – Access data from anywhere in real time.
-
Higher Quality – More consistent parameters, fewer defects.
First Steps to Implement IIoT
-
Assess your equipment and data needs
-
Set priorities: which data matters most?
-
Install sensors and begin data collection
-
Choose a platform (e.g., Siemens MindSphere, PTC ThingWorx)
-
Train your team
-
Start with a pilot project
What You Can Automate Today
-
CNC monitoring
-
Alerts for vibration, temperature
-
Downtime tracking
-
Tool wear prediction
-
Real-time quality control
Conclusion
IIoT is not the future — it’s the present. Starting with one machine or area, you can scale up to a fully connected smart workshop.
How to Properly Maintain and Calibrate Laser Systems for Cutting Precision
How to Properly Maintain and Calibrate Laser Systems for Cutting Precision
Introduction
Laser cutting machines provide incredible accuracy—but only if they are regularly maintained and precisely calibrated. Dust, heat, vibrations, and optical misalignments can degrade performance. Preventive care is not optional—it’s essential.
1. Why Maintenance Matters
Poor maintenance leads to:
-
Inaccurate cuts and waste;
-
Increased wear of optics and moving parts;
-
Safety risks and overheating;
-
Costly repairs and downtime.
2. Daily Maintenance
-
Clean lenses and mirrors with isopropyl alcohol and lint-free cloths.
-
Check the focus manually or with an autofocus tool.
-
Inspect the cooling system: coolant levels and leaks.
-
Remove dust from the cutting area and ventilation.
3. Weekly and Monthly Tasks
Weekly:
-
Tighten loose mounts and check optical alignment.
-
Clean air filters and fan blades.
-
Inspect belt tension and axis movements.
Monthly:
-
Recalibrate axes (X/Y).
-
Replace worn optical parts if needed.
-
Test laser spot alignment and symmetry.
4. Calibration Steps
-
Optical path calibration: Fire test pulses at corners to check beam alignment.
-
Focus testing: Cut test lines at varying focal distances.
-
Axis calibration: Cut a grid or circle and measure for geometric distortion.
-
Software calibration: Adjust motor steps per mm, backlash compensation, and scaling.
5. Common Mistakes
Mistake | Consequence |
---|---|
Cleaning optics with paper or fingers | Scratches, heat distortion |
Skipping coolant maintenance | Overheating and laser damage |
No alignment after moving the machine | Misalignment and cut errors |
6. Safety Guidelines
-
Disconnect power before maintenance.
-
Wear gloves and laser safety glasses.
-
Store lenses in dry, dust-free containers.
How to Choose the Optimal Cooling System for CNC Equipment
How to Choose the Optimal Cooling System for CNC Equipment
In precision machining, temperature plays a critical role. Overheating of tools and workpieces leads to deformation, accelerated wear, and poor surface finish. A well-designed cooling system is essential not just for tool longevity, but for production stability and quality.
This article overviews the main types of CNC cooling systems, their advantages, limitations, and which to choose based on your material and process.
Why Is Cooling So Important?
During high-speed cutting, friction generates heat that can cause:
-
Tool wear and loss of cutting edge sharpness
-
Dimensional inaccuracies in the workpiece
-
Thermal expansion or warping
-
Surface roughness or burns
-
Process instability
Cooling systems remove heat, reduce friction, and improve chip evacuation.
Main Types of Cooling Systems
1. Liquid Coolant (Emulsion, Oil)
The most common system — coolant is sprayed directly onto the cutting zone.
Advantages:
-
Efficient heat removal
-
Helps flush away chips
-
Reduces tool wear and friction
Disadvantages:
-
Requires filtration and maintenance
-
Potential for corrosion
-
Higher environmental impact
Best for:
Steel, titanium, nickel alloys, deep or intensive cutting processes.
2. Minimum Quantity Lubrication (MQL)
A fine aerosol of lubricant is sprayed in minimal quantities directly into the cutting zone.
Advantages:
-
Clean working area
-
Low coolant consumption
-
Environmentally friendly
Disadvantages:
-
Less effective heat control than liquid
-
Requires precise nozzle positioning
Best for:
Aluminum, light alloys, plastics, where dry machining or low-maintenance setups are preferred.
3. Compressed Air Cooling
Air is blown into the cutting zone to cool the part and clear chips.
Advantages:
-
No coolant required
-
Simple and clean
-
Low maintenance
Disadvantages:
-
Less cooling efficiency
-
Not suitable for hard materials
Best for:
Plastics, graphite, soft metals, or dry finishing operations.
4. Cryogenic Cooling (Liquid Nitrogen, CO₂)
Applies ultra-low temperatures directly to the cutting area using gases.
Advantages:
-
Maximum tool life and surface quality
-
Ideal for superalloys
-
Environmentally neutral
Disadvantages:
-
High equipment and running cost
-
Requires gas storage and handling systems
Best for:
Nickel alloys, aerospace parts, medical machining, high-speed finishing.
How to Choose the Right System
1. Consider the Material:
-
Hard metals (titanium, steel) → Liquid or cryogenic
-
Aluminum, brass → MQL or liquid
-
Plastics → Air or dry
2. Cutting Intensity:
-
High speeds and feeds → Stronger cooling
-
Light finishing → Minimal or dry cooling is often enough
3. Shop Floor Conditions:
-
Is coolant recovery available?
-
Is part cleanliness critical (e.g. medical, electronics)?
4. Budget and Sustainability:
-
MQL reduces coolant cost
-
Cryogenics give excellent results but are costly
Conclusion
Choosing the right CNC cooling method is essential for efficiency, part quality, and tool life. There’s no one-size-fits-all solution — your materials, machines, and production goals must all be considered.
Need help configuring your cooling setup? UDBU specialists will help you find the best solution for your production.
Contact us to increase your machining performance and reliability.
Overview of New Materials for CNC Machining: From Composites to High-Strength Alloys
Overview of New Materials for CNC Machining: From Composites to High-Strength Alloys
Modern industries are actively adopting new materials that offer excellent strength-to-weight ratios, resistance to wear and corrosion, and improved performance under demanding conditions. However, machining these materials requires adjustments in tooling, cutting strategies, and cooling systems.
This article provides an overview of the most commonly used advanced materials, their benefits, machining challenges, and practical recommendations.
Carbon Fiber (CFRP)
Advantages:
-
High strength with low weight
-
Corrosion resistance
-
Excellent vibration damping
Challenges:
-
Abrasive wear of cutting tools
-
Risk of delamination
-
High sensitivity to vibrations
Recommendations:
-
Use diamond-coated tools (PCD)
-
Install dust extraction systems
-
Minimize cutting forces and vibrations
Titanium Alloy (e.g., Ti-6Al-4V)
Advantages:
-
High strength and corrosion resistance
-
Excellent strength-to-weight ratio
-
Biocompatible — widely used in medical and aerospace sectors
Challenges:
-
Poor thermal conductivity — overheating risk
-
Built-up edge on tools
-
Expensive material → high cost of errors
Recommendations:
-
Use carbide tools with TiAlN or AlCrN coating
-
Apply high-pressure coolant
-
Reduce feed rate, maintain moderate speed
Nickel Superalloys (Inconel, Hastelloy, Waspaloy)
Advantages:
-
Excellent high-temperature resistance
-
Outstanding corrosion protection
-
Dimensional stability under load
Challenges:
-
High cutting forces
-
Rapid tool wear
-
Tendency to work-harden
Recommendations:
-
Use wear-resistant carbide tools
-
Carefully monitor tool wear and cutting temperature
-
Use low depth and conservative cutting speeds
High-Strength Aluminum Alloys (7xxx series)
Advantages:
-
Lightweight with high mechanical strength
-
Good corrosion resistance
-
Common in aerospace and automotive industries
Challenges:
-
Chip buildup
-
Burr formation
Recommendations:
-
Use polished-flute cutters
-
Employ high spindle speeds, low axial forces
-
Prefer dry or MQL cooling
Engineering Plastics (PEEK, PTFE, Delrin)
Advantages:
-
Low weight and chemical resistance
-
Good electrical insulation
-
Easy to machine
Challenges:
-
Thermal deformation
-
Long, stringy chips
-
Low stiffness — prone to vibration
Recommendations:
-
Use sharp single-flute tools
-
Apply high spindle speed, low feed
-
Avoid overheating the material
Conclusion
Modern materials like composites, titanium, nickel alloys, and engineering plastics open new opportunities in design and manufacturing. However, successful CNC machining of these materials requires knowledge, preparation, and the right tooling.
UDBU can help you choose the optimal machining strategies, cutting tools, and equipment configurations.
Contact us today to improve your material processing efficiency.
Automation of Part Loading and Unloading: How to Improve Production Efficiency
Automation of Part Loading and Unloading: How to Improve Production Efficiency
Modern manufacturing demands speed, precision, and consistency. Automating part loading and unloading operations on CNC machines is no longer just an innovation — it's a key strategy for staying competitive. These solutions increase productivity, reduce downtime, and minimize the impact of human error.
Why Automate?
Manual loading/unloading is still common in many factories. But this can cause:
-
Errors due to operator fatigue
-
Machine downtime during manual handling
-
Increased risk of accidents and inconsistent results
Automation solves these issues by performing tasks faster, safer, and more consistently.
What Systems Are Used?
1. Robotic Manipulators
-
6-axis industrial robots — for complex tasks and heavy parts
-
Gantry/portal robots — ideal for bulky or large items
-
Collaborative robots (cobots) — safe, easy to program, and perfect for SMEs
2. Conveyor Systems
-
Roller conveyors — for flat and heavy parts
-
Belt conveyors — for general-purpose handling
-
Modular conveyors with sorting — for mixed part production
Integration with CNC Machines
To integrate with CNC equipment, automation systems need:
-
Communication protocols (e.g. OPC UA, Ethernet/IP)
-
Compatible CNC controllers
-
Safety systems: barriers, guards, and emergency stops
Logic can be handled via PLC or directly within the CNC software.
Benefits of Automation:
-
Lower labor costs
-
Productivity boost (up to 50%)
-
Stable, repeatable quality
-
24/7 lights-out manufacturing
-
Better working conditions & safety
Real-World Examples:
-
Aluminum parts production: robot implementation increased output by 40%
-
Small batch production: cobots enabled unmanned night shifts with minimal setup time
Final Thoughts:
Automation isn’t as complicated as it seems — especially with UDBU by your side. We’ll help you select and integrate the right solution for your space, budget, and workload.
Contact us today and boost your productivity.
English: Laser or Cold Saw for Pipe Cutting – What to Choose?
English: Laser or Cold Saw for Pipe Cutting – What to Choose?
When choosing pipe cutting equipment, many factors matter: precision, speed, cost, material type, and more. Let’s compare two popular methods — laser cutting and cold saw cutting — to help you decide which is right for you.
Laser Cutting
Advantages:
-
High precision and edge quality. Clean cuts with minimal burrs; often no post-processing required.
-
Flexibility. Ideal for cutting complex shapes, holes, and contours.
-
Automation-ready. Modern laser machines easily integrate into production lines.
Disadvantages:
-
Expensive equipment and maintenance.
-
Limited with thick pipes.
-
Requires skilled operator.
Best for: high-precision and small-batch production, cutting stainless steel, aluminum, copper, and other non-ferrous metals.
Cold Saw Cutting
Advantages:
-
Affordable. Lower equipment and maintenance costs.
-
Efficient with thick-walled pipes.
-
Easy to operate and maintain.
Disadvantages:
-
Limited to straight cuts.
-
Less precision. May require additional finishing.
-
More noise and material waste.
Best for: mass production, cutting ferrous metals, straightforward operations with large-diameter pipes.
Summary Table:
Factor | Laser Cutting | Cold Saw Cutting |
---|---|---|
Precision | Very high | Medium |
Speed | Moderate | High (on straight cuts) |
Equipment Cost | High | Medium/Low |
Complex Shapes | Yes | No |
Maintenance | Complex/Expensive | Simple |
Conclusion
If precision and versatility are top priorities, go with laser cutting. If you need cost-effective, high-speed cutting for standard operations, cold saw is your choice.
Need help choosing equipment? Contact our team — we’ll help you find the best solution for your project.
Optimising CNC Lathe Operations: Tips for Enhanced Precision and Efficiency
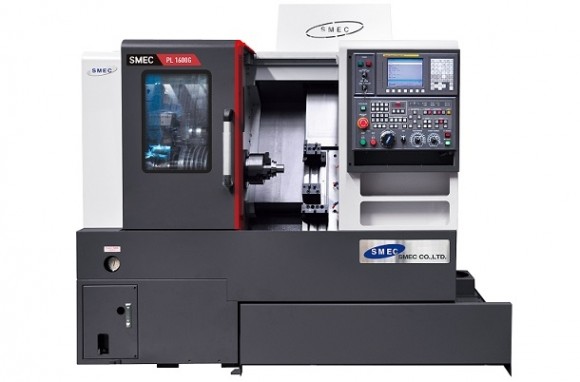
Optimising CNC Lathe Operations: Tips for Enhanced Precision and Efficiency
In modern manufacturing, CNC lathes are essential machines that ensure high precision and repeatability. However, even the most advanced equipment requires proper maintenance, setup, and workflow organisation to reach peak performance. In this article, we share practical tips to help optimise your CNC lathe operations for improved precision and efficiency.
1. Regular Machine Maintenance
Routine maintenance is a critical factor in CNC machine performance.
-
Check lubrication systems and fluid levels.
-
Clean guideways and working surfaces of chips and dust.
-
Inspect spindles and carriages for wear or vibration.
2. Tool Calibration
Incorrect tool positioning can lead to inaccuracies in the final product.
-
Regularly calibrate and reset tools.
-
Check tool edge condition and wear.
-
Inspect automatic tool changers (if applicable).
3. G-Code and Software Optimisation
Efficient G-code programming can significantly reduce cycle times and errors.
-
Review tool paths to eliminate unnecessary movements.
-
Use optimisation features in your CAM software.
-
Implement adaptive cutting for complex materials.
4. Workpiece Preparation
Improperly prepared or clamped workpieces can cause issues during machining.
-
Ensure proper clamping and alignment.
-
Use suitable holders or chucks.
-
Verify the size and shape of the raw material before processing.
5. Monitoring and Data Analysis
Modern CNC machines often include monitoring tools for performance tracking.
-
Use data to evaluate cycle times and tool wear.
-
Identify workflow bottlenecks or inefficiencies.
-
Improve processes based on real-time performance data.
Conclusion
CNC lathes deliver optimal results only when properly maintained and operated. With the right setup, high-quality tools, and consistent monitoring, you can significantly improve your production quality, speed, and reliability.
Looking to upgrade or buy a new CNC lathe? Explore our product selection here
How to Choose the Right CNC Software for Your Manufacturing Needs
How to Choose the Right CNC Software for Your Manufacturing Needs
CNC (Computer Numerical Control) technology has become a core part of modern manufacturing. To operate CNC machines successfully, you need not only quality hardware but also the right software tailored to your specific needs. Here's how to choose the best CNC software for your operations:
1. Understand Your Production Requirements
Before choosing software, consider:
-
What materials you work with (wood, metal, plastic, etc.)
-
What types of CNC machines you use (milling, laser, plasma, lathe, etc.)
-
How complex your work is (simple cuts or detailed 3D models)
-
Your production scale (custom, small-batch, or mass production)
🛠️ 2. Main Types of CNC Software
Software Type | Function |
---|---|
CAD (Computer-Aided Design) | For creating designs and technical drawings |
CAM (Computer-Aided Manufacturing) | Generates tool paths based on CAD designs |
G-code Editors/Simulators | Allows code review and optimization before machining |
Some platforms offer integrated CAD/CAM solutions.
3. Popular CNC Software Options
-
Fusion 360 – Combines CAD and CAM; great for prototyping and small-scale production
-
SolidWorks + SolidCAM – Ideal for advanced 3D operations
-
Vectric (VCarve, Aspire) – User-friendly and great for woodworking
-
Mach3 / Mach4 – CNC machine control software for hobbyists and small workshops
-
SheetCAM – Designed for plasma, laser, and oxy-fuel cutting
4. What to Consider When Choosing
- Ease of use – How quickly your team can learn the software
- Compatibility – With your machines and controllers
- Support & documentation – Availability of tutorials and tech help
- Cost & licensing – One-time, subscription, or free options
- Software updates – Active development and bug fixes
5. Looking Ahead: Automation & Cloud Integration
Modern CNC software often includes:
-
Cloud storage for designs
-
Automated workflows
-
Integration with ERP/logistics systems
-
Production data analytics
These features are especially useful for scaling and optimizing production.
Conclusion
Choosing the right CNC software is key to efficient, precise, and profitable manufacturing. Whether you're a hobbyist or a large-scale producer, the right tool helps you get the most from your CNC machines.
Ensuring Stability in High-Speed Laser Cutting: From Cutting Strategy to Collision Prevention
Ensuring Stability in High-Speed Laser Cutting: From Cutting Strategy to Collision Prevention
High-speed laser cutting offers unparalleled precision and efficiency in metal fabrication. However, achieving optimal performance requires a strategic approach that encompasses cutting strategies and advanced collision prevention techniques.
Strategic Planning: Optimising Cutting Paths
Effective cutting strategies are foundational to maintaining stability during high-speed operations:
-
Contour Analysis: Prior to cutting, evaluate the geometry of the material to identify potential challenges such as narrow bridges or intricate internal contours that may compromise stability.
-
Sequencing: Plan the cutting sequence to minimize the movement of the laser head over already cut areas, reducing the risk of collisions with fallen or shifted parts.
-
Lead-In and Lead-Out Paths: Design these paths to avoid intersecting with critical areas, ensuring smooth transitions and reducing mechanical stress.
-
Utilizing Simulation Software: Employ advanced CAM software to simulate the cutting process, allowing for the identification and rectification of potential issues before actual cutting begins.
Advanced Collision Prevention Technologies
Modern laser cutting systems incorporate sophisticated technologies to prevent collisions:
-
Intelligent Collision Avoidance (ICA): Developed by Lantek, ICA detects unstable contours and assigns micro-cuts at their ends. This proactive approach ensures that parts are securely fastened before the laser head passes over them, significantly reducing the risk of collisions .
-
Active Anti-Collision Systems: Bodor's laser machines are equipped with active anti-collision functions that utilize high-speed Z-axis adjustments to avoid obstacles. This system can detect potential collisions and respond dynamically, enhancing safety and efficiency .
-
Laser Distance Sensors: Wenglor's Time-of-Flight sensors measure distances up to 10 meters, providing real-time data to prevent collisions in automated systems like gantry loaders .
-
Machine Vision and AI Integration: Implementing machine vision systems equipped with AI allows for real-time monitoring and adjustment of the cutting process, identifying and correcting deviations that could lead to collisions .
Maintenance and Calibration
Regular maintenance and calibration are crucial to ensure the longevity and stability of laser cutting systems:
-
Routine Inspections: Conduct regular checks on the laser head, focusing on components such as lenses and mirrors, to ensure optimal performance.
-
Calibration: Periodically calibrate the laser system to maintain cutting accuracy and prevent misalignments that could lead to collisions.
-
Software Updates: Keep the cutting software up to date to leverage the latest advancements in collision prevention algorithms and features.
Benefits of Implementing Advanced Strategies
Adopting comprehensive cutting strategies and advanced collision prevention technologies offers several advantages:
-
Increased Productivity: Minimizing downtime due to collisions leads to more consistent and efficient operations.
-
Cost Savings: Reducing the frequency of repairs and part replacements lowers operational costs.
-
Enhanced Safety: Proactive collision avoidance measures protect both equipment and personnel.
-
Improved Quality: Stable cutting processes result in higher-quality finished products with fewer defects.
By integrating thoughtful cutting strategies with cutting-edge collision prevention technologies, manufacturers can achieve stable and efficient high-speed laser cutting operations.
How to Choose a Compressor for Laser or Plasma Cutting: Key Criteria and Tips
How to Choose a Compressor for Laser or Plasma Cutting: Key Criteria and Tips
When working with laser or plasma cutters, it’s not just the cutting head that matters — auxiliary equipment like compressors plays a crucial role. A well-chosen compressor ensures cutting precision, machine longevity, and process stability.
Here’s what you should consider when selecting a compressor for your cutting system.
Why Do You Need a Compressor?
The compressor provides compressed air that:
-
Removes smoke and molten material from the cutting zone;
-
Cools the cutting area, protecting components from overheating;
-
Protects optics (for lasers) from contamination;
-
Forms plasma in high-pressure plasma cutting.
Clean, stable air = clean, consistent cuts.
Key Selection Criteria
1. Air Flow Rate (L/min or m³/h)
Your compressor should meet or slightly exceed your machine’s requirements:
-
Plasma: 200–500 L/min;
-
Lasers: 50–300 L/min.
Also factor in:
-
Hose and fitting losses;
-
Continuous operation needs;
-
Future equipment expansion.
2. Output Pressure (bar/MPa)
-
Lasers: 5–7 bar;
-
Plasma: 6–8+ bar.
Choose a unit with pressure reserve.
3. Air Quality
Especially critical for lasers:
-
Use filters and moisture separators;
-
For high-end needs, install an air dryer.
4. Compressor Type
-
Piston compressors – affordable, but noisy and less durable;
-
Screw compressors – more expensive, but quieter and made for continuous work.
5. Air Tank (Receiver)
Larger tanks provide smoother performance:
-
Plasma: 50–200 L;
-
Laser: 30–100 L.
Additional Tips
-
Consider noise level, especially for workshops;
-
Perform regular maintenance (oil, filters, condensate drain);
-
Ensure proper power supply (220V or 380V);
-
Allow for at least 20% performance headroom.
Conclusion
The right compressor protects your machine and boosts performance. Don’t cut corners — analyze your needs and choose wisely.
How to Choose a Laser Cutting Machine? 5 Key Factors
How to Choose a Laser Cutting Machine? 5 Key Factors
Metalworking, Manufacturing Equipment
Laser Cutting – The Foundation of Modern Manufacturing
Laser cutting has become one of the most efficient and precise methods for processing metals and other materials. However, before purchasing a laser cutting machine, it's important to understand which factors influence its performance and suitability for specific needs.
1. Laser Type and Power
Laser power (typically from 1 kW to 12 kW) determines the thickness of the material that can be cut. CO₂ lasers are ideal for non-metallic materials, while fiber lasers offer faster and more efficient metal processing.
2. Working Area Size
Choose a machine with a working area that suits your production needs – whether it's 1300x900 mm for workbenches or larger sheet processing systems.
3. Cutting Speed and Precision
The faster and more precise the machine, the shorter the production cycle. It's also important to assess the quality of linear guides and servo motor systems, as they affect the final result.
4. Control System and Ease of Use
Modern control systems with intuitive software ensure easy machine setup and integration with CAD/CAM tools.
5. Service and Maintenance
When choosing a machine, also consider the technical support provided by the manufacturer or distributor, availability of spare parts, and training opportunities.
Our Recommendation
UDBU offers a wide range of laser cutting machines from trusted manufacturers – with varying power levels, applications, and automation options. We help select the most suitable solution for both small workshops and manufacturing companies.
Why Choose TIG Welding? Advantages and Applications in Metalworking
Why Choose TIG Welding? Advantages and Applications in Metalworking
Welding, Metalworking Technologies
What is TIG Welding?
TIG (Tungsten Inert Gas) welding is a process that uses a tungsten electrode and an inert gas (usually argon) to produce a high-quality weld. This technology is especially suitable for metals that require precise and aesthetic processing.
Advantages of TIG Welding
-
High weld quality – clean and strong welds with no spatter
-
Better control – the welder can precisely control temperature and weld formation
-
Ideal for thin materials – reduced heat input minimizes deformation risk
-
Spatter-free – unlike MIG welding, TIG ensures a cleaner working environment
Where is TIG Welding Used?
-
Manufacturing of stainless steel components
-
Assembly of aluminum structures
-
Welding of automotive and motorcycle parts
-
Industrial equipment requiring high precision
UDBU TIG Welding Solutions
We offer modern TIG welding machines suitable for both industrial and workshop use. Contact our team to select the equipment best suited to your needs.
Waterjet Cutting vs. Laser Cutting: Which Technology Should You Choose?
Waterjet Cutting vs. Laser Cutting: Which Technology Should You Choose?
In the world of industrial material processing, choosing the right cutting technology is key to achieving precision, efficiency, and cost-effectiveness. Two of the most popular methods — waterjet cutting and laser cutting — each have their own advantages and limitations. Let’s explore the differences and help you determine which one suits your needs.
What is Waterjet Cutting?
Waterjet cutting is a method where a high-pressure stream of water mixed with abrasive powder (usually garnet) is used to cut materials. This stream can even slice through metal several centimeters thick.
Advantages of waterjet cutting:
-
Cold cutting: No heat is involved, so there’s no warping or material alteration.
-
Wide range of materials: Suitable for metals, stone, ceramics, glass, composites, and even food.
-
High precision: Excellent for complex shapes and fine details.
-
Eco-friendly: Minimal waste and no harmful fumes.
Disadvantages:
-
Slower than laser cutting
-
Moisture: The process is wet, which can be problematic for some production environments.
-
Higher maintenance cost: High-pressure pumps and abrasives require regular upkeep.
What is Laser Cutting?
Laser cutting uses a focused beam of light to melt, vaporize, or burn through material. It is known for high speed and accuracy when cutting metals and some non-metallic materials.
Advantages of laser cutting:
-
High processing speed, especially on thin metals.
-
Excellent edge quality: Minimal kerf and almost no burrs.
-
Highly automatable: Easily integrated into production lines.
Disadvantages:
-
Thickness limitations: Less effective for materials thicker than 20–25 mm (depending on laser power).
-
Heat-affected zone: May cause warping or thermal changes in the material.
-
Limited material compatibility: Not ideal for reflective or insulating materials like copper or ceramics.
Comparison Table
Characteristic | Waterjet Cutting | Laser Cutting |
---|---|---|
Type of action | Mechanical (water + abrasive) | Thermal (laser beam) |
Material thickness | Up to 300 mm | Up to 25 mm (depends on laser type) |
Material types | Almost all, including glass and ceramics | Mainly metals and plastics |
Precision | High | Very high |
Processing speed | Medium | High |
Environmental impact | High (clean process) | Medium (some fumes) |
Equipment cost | High | Medium to high |
How to Choose?
-
Working with thick or heat-sensitive materials? Go with waterjet.
-
Need speed and precision on thin metals? Choose laser.
-
Looking for versatility? Waterjet is more flexible but costlier to maintain.
Conclusion
Each technology has its strengths. The right choice depends on your specific production needs: material type, thickness, required precision, and budget. Ideally, consult an expert or test both technologies on your materials.
How to Avoid Vibrations During Milling on the Holzmann BF 500DDRO
How to Avoid Vibrations During Milling on the Holzmann BF 500DDRO
The Holzmann BF 500DDRO milling machine is a modern, versatile unit designed for precise metalworking. Thanks to its heavy cast-iron frame and high-quality components, it provides excellent stability. However, even with this kind of equipment, it's essential to follow proper setup procedures to reduce vibration and achieve the best possible results.
Main Causes of Vibration
-
Insufficient system rigidity
-
Unbalanced tooling
-
Incorrect cutting parameters
-
Uneven workpiece surface
How to Minimize Vibration on the BF 500DDRO
-
Use rigid and stable clamping systems
-
Minimize tool overhang
-
Optimize cutting speed, feed rate, and depth
-
Apply coolant for smoother cutting and reduced friction
Conclusion
When properly set up and maintained, the BF 500DDRO delivers stable and accurate machining with minimal vibration. Regular maintenance and correct use will extend the lifetime of both the machine and the tooling.
How to Choose a Metalworking Machine for a Startup: Minimum Cost — Maximum Efficiency
How to Choose a Metalworking Machine for a Startup: Minimum Cost — Maximum Efficiency
Starting a business in metalworking means balancing your budget and efficiency. It’s crucial to choose equipment that can handle the necessary tasks without causing excessive costs. Here are some tips for choosing a machine for a small-scale metalworking business.
1. Define the tasks
Start by identifying the main operations the machine will perform:
-
Metal cutting
-
Engraving and marking
-
Welding
-
Milling or drilling
Each task requires specific equipment, and there are very few true all-in-one solutions.
2. Estimate your production volume
For small batches, compact tabletop machines are usually sufficient. They are cheaper, require less space, and are easier to set up.
Larger production volumes may require semi-automatic or fully automatic machines for continuous and precise operation.
3. Consider dimensions and power usage
Make sure your workspace can accommodate the machine and that your power supply can handle it. Smaller machines often consume under 2 kW and don’t need industrial power.
4. Look for versatility
If your budget is limited, opt for a machine that can handle various materials or tasks. This increases flexibility and broadens your service offering.
5. Think about support and training
Even the best machines can break down. Choose a supplier that offers technical support and training. This reduces downtime and saves on maintenance costs.
In summary
Choosing a machine is about balancing cost, functionality, and workspace. Compact, energy-efficient models with well-defined capabilities are often the best choice for startups.